A single suction pump is very popular. However, it has its disadvantages as well. This article will explain why double pumps are better than singles. Listed below are some of the most common types of double pumps and how to choose one. You can choose whichever pump suits your needs the best. If you are still unsure, read on to learn about the advantages and disadvantages of both types. Here are some of the features of each.
Single suction pump
A single suction pump has a single stage, and is commonly referred to as an end-auction pump. This type of pump is powered by a shaft that rotates the impeller at a high speed, which forces the pre-filled fluid to move between the impeller's blades. This process increases the static pressure in the fluid and increases the flow rate. Single-stage pumps are used for a variety of applications, including water supply, industrial applications, and heating and air conditioning.
Depending on the size of the system, one type of single-stage pump may be best. A small-sized system may be best served by an end-suction pump, which requires less floor space in the plant room. Medium-sized systems might benefit from a vertical in-line pump or a split-case pump, but these may be too big for the system. To determine which type of pump is right for your application, look for the following characteristics:
The pressure rise and side clearance of the pump can affect its performance. With increased side clearance, the maximum absolute velocity of the impeller channel shifts toward the trailing edge. This is due to increased mass flow above the impeller's tip, which impedes core flow. If the pressure is too high, the pump will slow down to compensate for the increased pressure. For this reason, a pressure sensor is necessary to ensure proper pump performance.
A double-suction pump can be an efficient solution for many applications. The efficiency of a double-suction pump is 4.14% higher, and the head of a single-suction pump is 3.5% higher. The size of a double-suction pump is more space-efficient, but it is still expensive. Both types of pumps have similar cavitation performance. However, the size of the vertical pumps makes servicing difficult.
Alternatively, a single-stage centrifugal pump can be a multi-stage pump, which has two or three impellers. Single-stage pumps are characterized by their small size, high speed, and low pressure head. Depending on the needs of the application, a single-stage centrifugal pump can also be categorized as a horizontal or vertical pump. If the suction line is near the grade, low-NPSH options may be available. Alternative suction arrangements may include an inlet at the top of the pump, or a connection to a vessel elevated above the pump.
Another popular style of single-stage pumps is the horizontal split-case pump. Horizontal split-case pumps are similar to end-suction pumps, but feature a large, heavy impeller. Split-case pumps typically have a longer lifespan and are heavier. However, the cost of maintenance for end-suction pumps can easily outweigh the savings from the initial cost. With horizontal split-case pumps, it is easy to remove the top half of the pump casing to access the internal components. Unlike the end-suction pump, they are designed to handle large water flows.
A double-stage pump has two impellers that are back-to-back. This design allows it to handle large flows and high head. A double-stage pump has two suction chambers and is used in many applications. They are based on the same principle as single-stage pumps, but have different cavitation characteristics. If you are considering investing in a centrifugal pump, you should know about its features.
One of the most important considerations in selecting an open-system pump is the net positive suction head. This refers to the pressure at the pump's inlet. If the pump fails at this point, it is usually due to a combination of flow instability and overheating. Moreover, it's not possible to use a single-suction pump in dry conditions, so you'll need to fill the pump before using it. Another type of fluid that can damage a centrifugal pump is high-density liquid. This fluid will not flow through a centrifugal pump because the higher density of the liquid forces more effort to move it and creates less ideal conditions for performance.
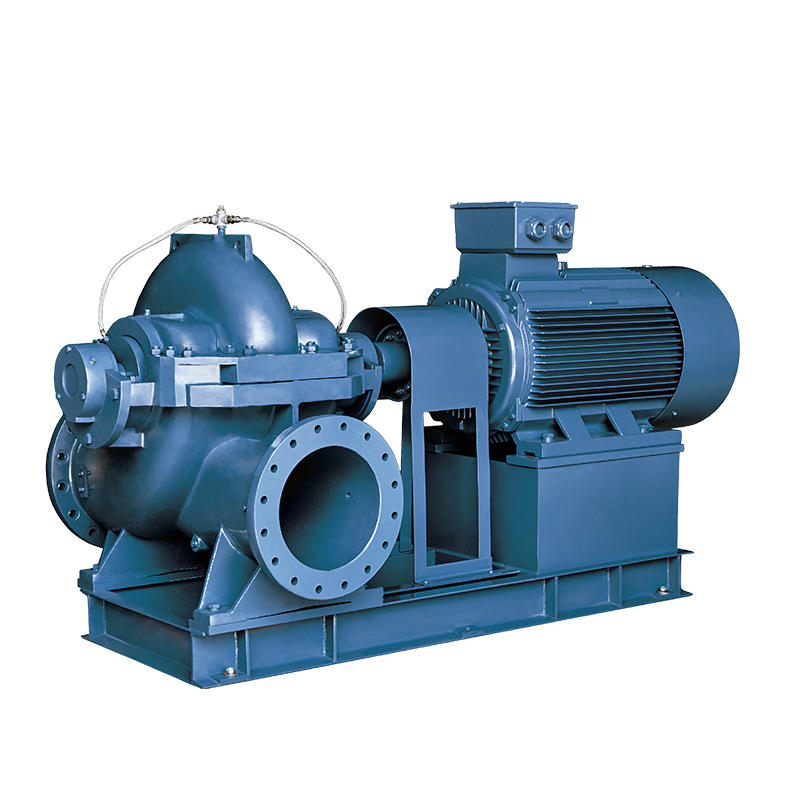